Sustainability at D3O
Our sustainability vision is to save lives, while continually striving to improve our environmental, social, and economic sustainability.
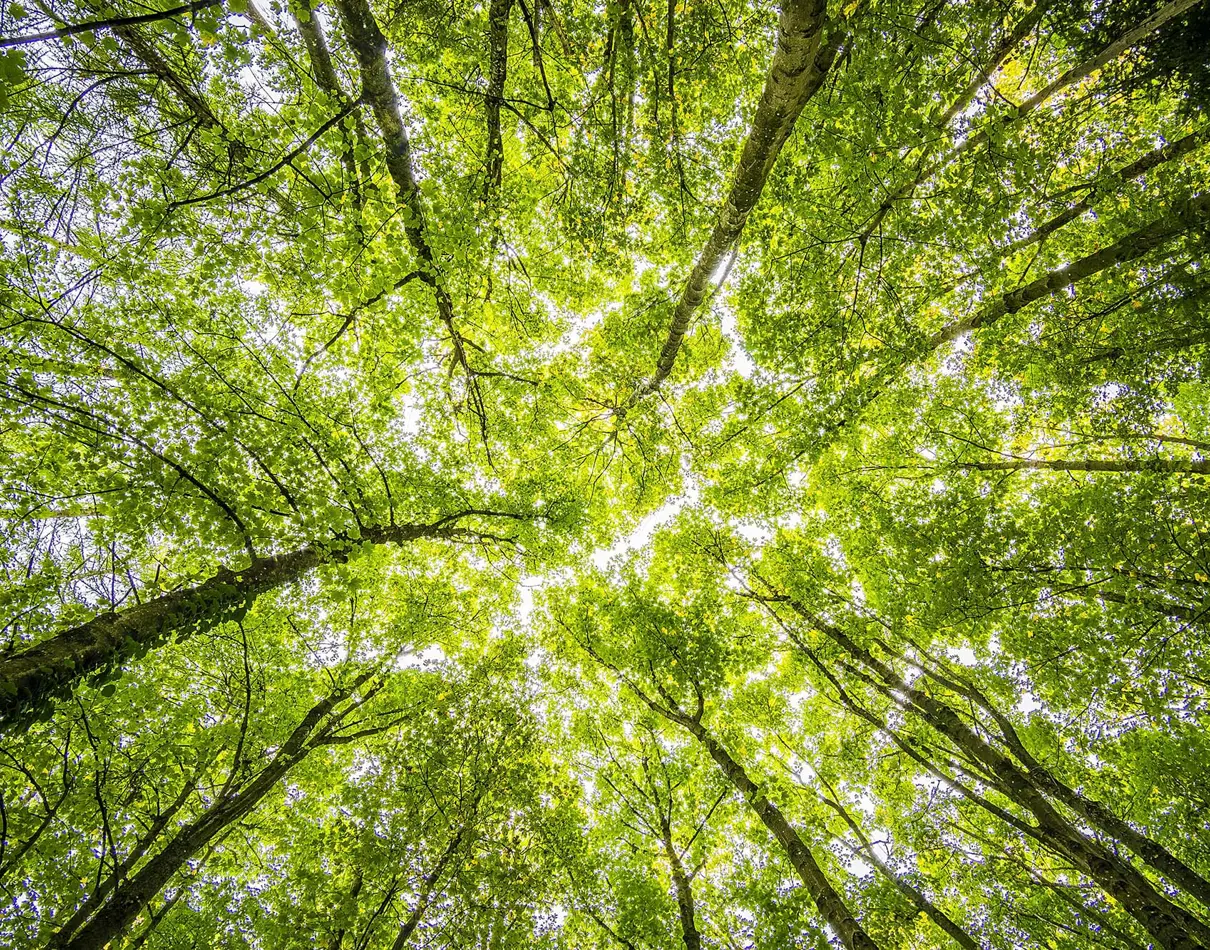
The company’s commitment to sustainable practices spans 3 key areas, which it undergoes annual audits on:
Environmental
D3O is committed to sustainability across its entire product lifecycle. Our products are designed for reuse and compliant with global safety standards. We are committed to minimizing our carbon footprint, and our company adheres to strict regulations such as REACH. D3O’s manufacturing process minimizes material use, energy consumption, and waste, while our supply chain uses eco-friendly packaging and limits air freight.
Social
D3O prioritizes the health, safety, and well-being of our employees, users, and partners, offering comprehensive benefits, personalized training, and a discrimination-free workplace. We are committed to social responsibility, and actively engage with communities through industry partnerships, outreach programs, and employee volunteering initiatives.
Governance
D3O has developed extensive governance policies covering employee and supplier codes of conduct, data protection, and corporate governance. Our business management system is certified to ISO 9001 2015, and our suppliers are validated to ensure compliance with social standards such as SEDEX and SMETA.
![Umbraco.Cms.Core.Models.MediaWithCrops`1[Umbraco.Cms.Web.Common.PublishedModels.Image]](https://cdn.d3o.com/media/2760/fox_mt_gloves_crop.jpg?width=1996&height=1042&format=webp&v=1dbbff82ebe2710)
Environmental
D3O® products are developed to meet relevant industry performance and safety standards around the world (including NOCSAE, ISEA, CE and UKCA) and are tested and certified by internationally recognised independent labs including SATRA, TUV and NPL. D3O® products are non-sacrificial and built for re-use, time and time again.
D3O identifies and prioritises ways it can significantly reduce its environmental footprint in the production, distribution, use, and end of life of its materials and products, through the use of a Life Cycle Assessment (LCA) tool. The LCA framework is based on ISO standards and aligned with the EU EF methodology.
Materials
D3O’s environmental management has demonstrated that the single most important area of influence in reducing its greenhouse gas emissions is its materials. D3O uses recycled and plant-based (also known as bio-based) content in its own and partner products, in lieu of fossil fuel-derived content, where possible.
Material reformulation to optimise material consumption and product performance has allowed D3O to achieve up to 9% reduction in CO2 emissions across our bestselling products. Nearly 70% of D3O’s active material portfolio including its most in-use materials D3O® Bio, ST, XTi, AeroMax and Aero, is plant-based. D3O works with its suppliers to verify that the plant-based content used is not in competition with food sources.
D3O® Zero™ and the fabrics used in D3O® parts are produced from recycled materials and meet the Eco Global Recycle Standard (GRS), which certifies that all products processed in the entire supply chain have undergone the proper steps to ensure the integrity of the final product. D3O® Zero™ transforms unused material from our product manufacture into a high-performance recycled material, reducing industrial waste. The use of recycled materials in our fabrics reduces our consumption of petroleum as a raw material, and lowers carbon emissions, water usage and water pollution from manufacturing.
D3O® materials comply with European Regulation REACH, ensuring that our products protect human health and the environment from the use of chemicals. D3O® materials contain either safe levels of organotin or are organotin-free, and D3O® formulations and products meet current regulatory limits on PFAS. D3O’s research and development in this space continues, with sustainability a key consideration in R&D projects.
Manufacturing
D3O follows a design philosophy that centres on creating durable protective products with minimal environmental impact. This approach minimises the amount of material used in our products, which accounts for most of the product’s impact. D3O manufactures to order and recycles production waste back into its products where possible to further minimise waste.
Supply Chain
From a Supply Chain perspective, D3O has halved its waste rate from rejected products over the past 4 years. D3O uses recycled cardboard boxes and has removed unnecessary single-use plastic packaging in its bulk packaging for customers. Air freight happens by exception only, requiring senior management approval.
![Umbraco.Cms.Core.Models.MediaWithCrops`1[Umbraco.Cms.Web.Common.PublishedModels.Image]](https://cdn.d3o.com/media/2180/partner-support-banner-2024.jpg?width=1996&height=1042&format=webp&v=1dbbff82fb5cd80)
Social
D3O puts the health, safety and well-being of its employees, users, and its partners first. The company puts an emphasis on employee engagement and development through in-house exercise and meditation facilities, recognition and rewards for high performance, investment in personalised training as well as benefits such as an extended cycle to work scheme and private healthcare plan.
D3O is an Equal Opportunities employer and is committed to providing a working environment that is free from unlawful discrimination, victimisation or harassment on the grounds of colour, race, nationality, ethnic origin, sexual orientation, gender reassignment, religion, disability or age.
D3O gives back to its communities, notably through partnering with industry associations such as the International Safety Equipment Association (ISEA) and CE for the shaping of industry standards, to ensure that people around the world are better protected. Within the defence sector, D3O partners with outreach programs and humanitarian organisations such as National Industries for the Blind, VisionCorps, Industries for the Blind and the Warrior Protection and Readiness Coalition. D3O employees also have the ability to allocate time to volunteering within their local community.
![Umbraco.Cms.Core.Models.MediaWithCrops`1[Umbraco.Cms.Web.Common.PublishedModels.Image]](https://cdn.d3o.com/media/2609/mtb-banner-scott.jpg?width=1996&height=1042&format=webp&v=1dbbff82f9d6380)
Governance
D3O has a sustainability strategy in place which covers the development of sustainable products in collaboration with stakeholders such as customers, suppliers and employees. The company has well-developed governance policies covering employee and supplier codes of conduct, data protection, and corporate governance. The business management system within D3O is certified to ISO 9001 2015, to ensure sustained customer satisfaction during product realisation, delivering services and providing support functions that meet customers’ needs and expectations. D3O’s suppliers are validated to ensure compliance with social standards such as SEDEX and SMETA. Furthermore, D3O invests in ongoing research and development to remain at the forefront of protection, perfecting its offering in impact protection and extending its reach into battling the effects of vibration and fatigue.